O funcionamento das correias transportadoras é essencial para o bom andamento dos processos.
Apesar da sujeira, da poeira ou da forte vibração, a lubrificação ideal é necessária para evitar falhas no equipamento. Os reparos dispendiosos e as visitas de manutenção representam uma parte significativa dos custos operacionais, que podem ser minimizados significativamente com o uso de sistemas de lubrificação perma.
Desafios
As correias transportadoras de grande porte geralmente se estendem por longas distâncias e vários níveis e são de difícil acesso. O ideal é que a relubrificação seja feita com o equipamento em funcionamento. Muitos pontos de transferência só podem ser lubrificados com a ajuda de grades de passarela ou plataformas de trabalho e, por isso, são frequentemente negligenciados. A prevenção de acidentes e a segurança no local de trabalho devem ser garantidas em todos os momentos.
Os pontos de lubrificação geralmente são negligenciados porque estão localizados no alto, na parte traseira ou em locais com pouco espaço de manobra. O trabalho de manutenção nessas áreas durante a operação é extremamente perigoso e coloca em risco a segurança no local de trabalho.
A falta de lubrificação resulta em desgaste, leva à falha dos componentes do equipamento e reduz a produtividade e a eficiência econômica.
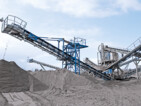
Sujeira e água não devem entrar nos pontos de lubrificação
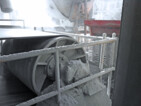
Sem paradas desnecessárias do equipamento devido à relubrificação
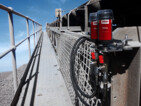
A segurança no local de trabalho deve ser garantida
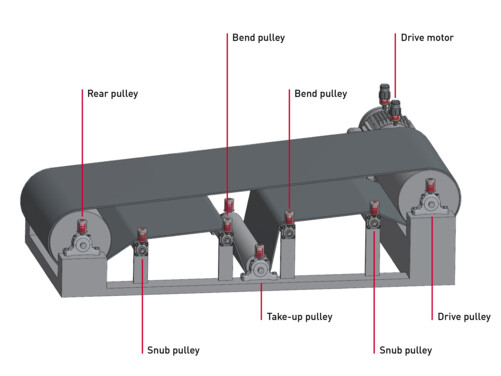
Pontos de lubrificação
As caixas de mancal com rolamentos esféricos são utilizadas principalmente em polias de acionamento e de curva.
Os rolamentos e as vedações das carcaças dos rolamentos devem ser permanentemente abastecidos com lubrificante.
Soluções
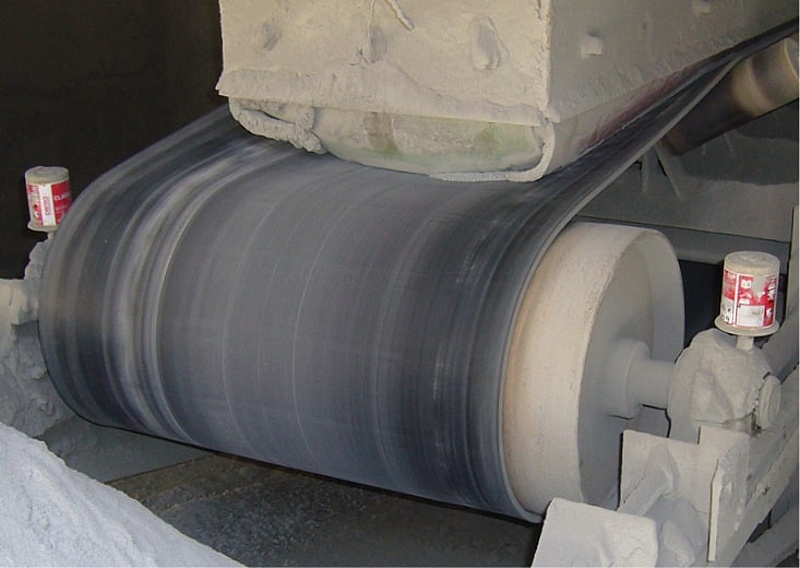
- Montagem fácil e rápida
- Para pontos de lubrificação com pouca vibração/choques
- Para pontos de lubrificação seguros e de fácil acesso
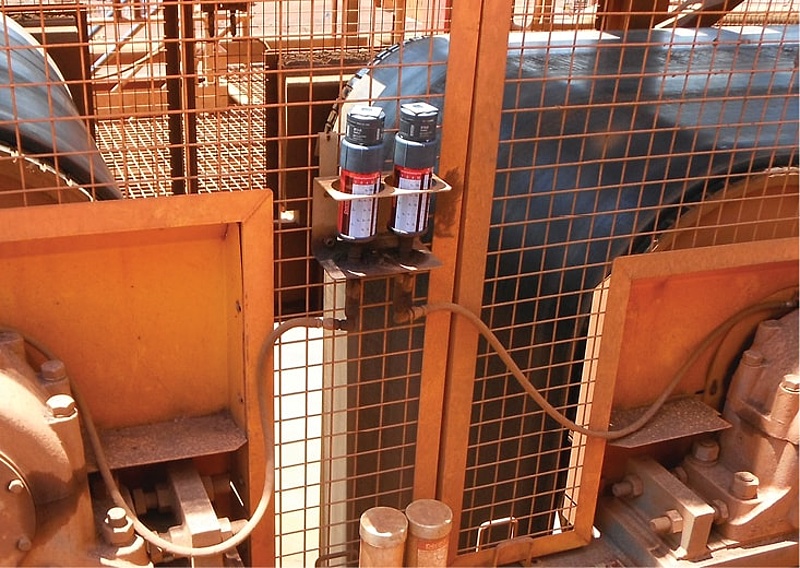
- Para pontos de lubrificação com fortes vibrações/choques (isolamento do sistema de lubrificação)
- Para pontos de lubrificação cujo acesso não é seguro: Montagem em áreas seguras
- Para pontos de lubrificação de difícil acesso
Dúvidas?
Vantagens da lubrificação automática
Menos contaminação
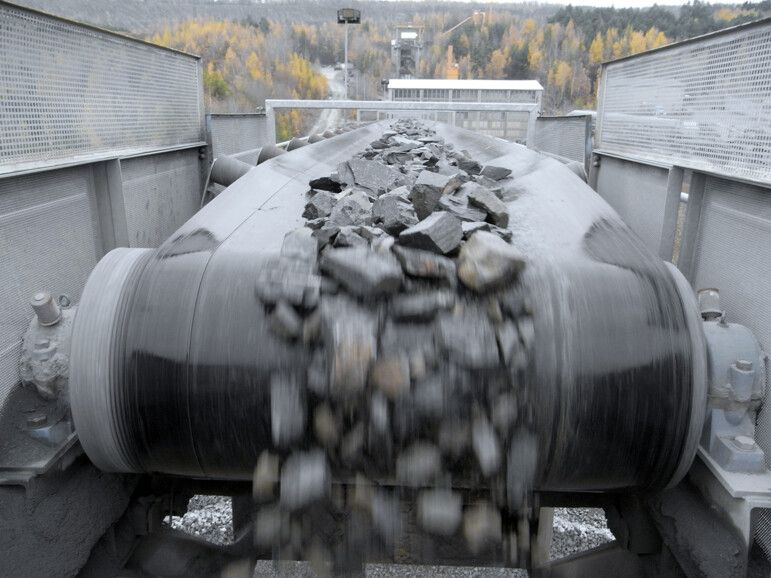
Sem interrupção
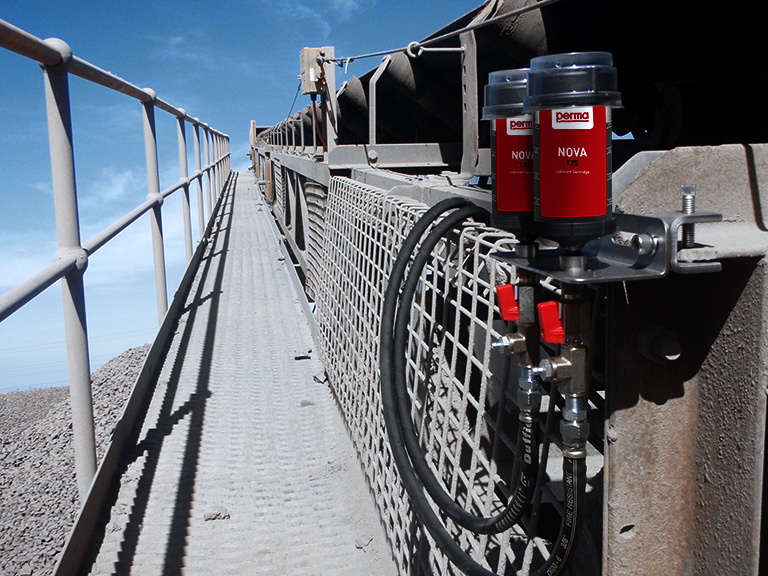
Prevenção de acidentes
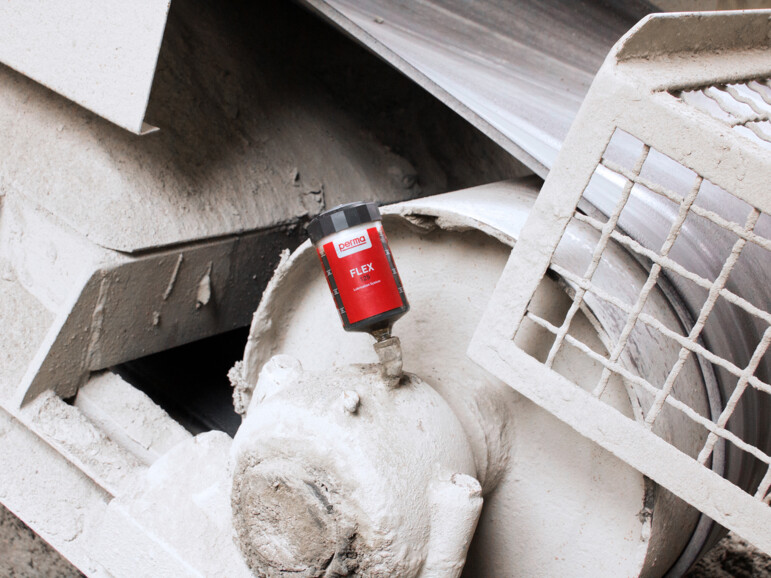
Menor impacto ambiental
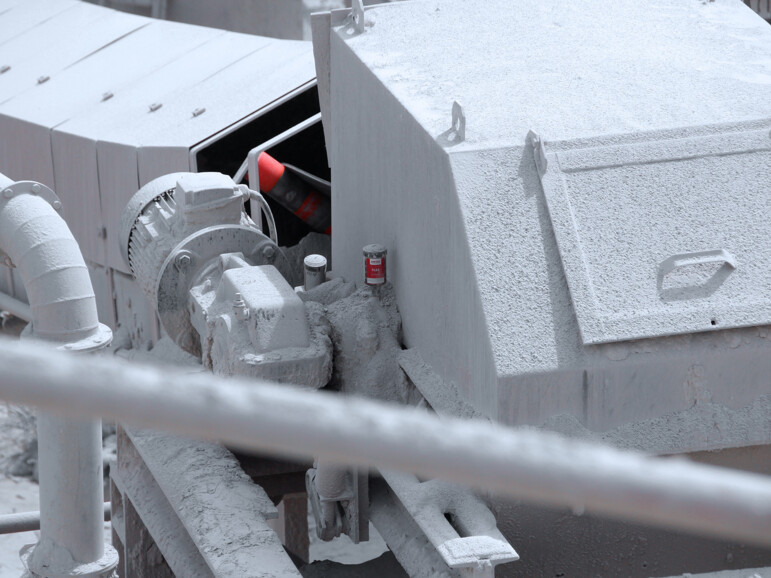
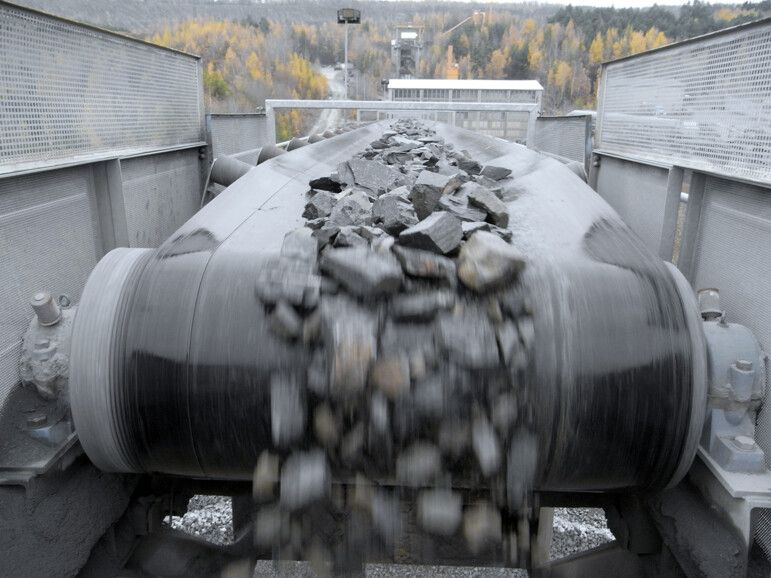
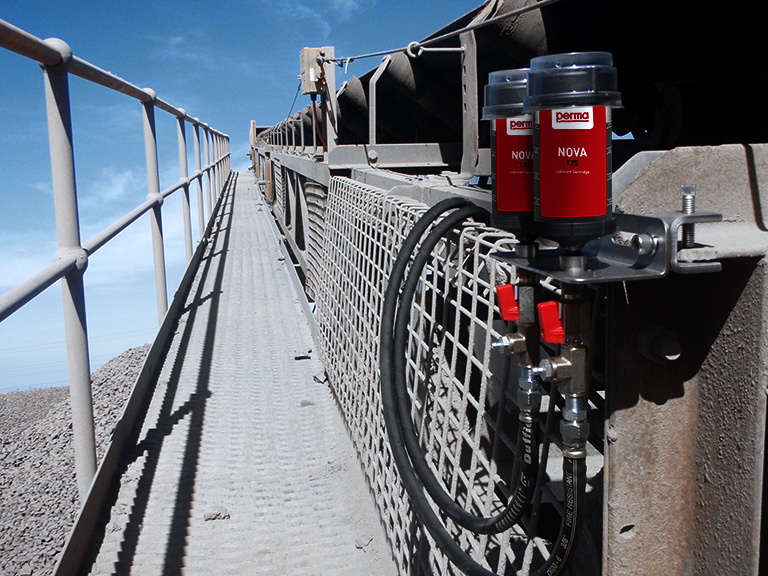
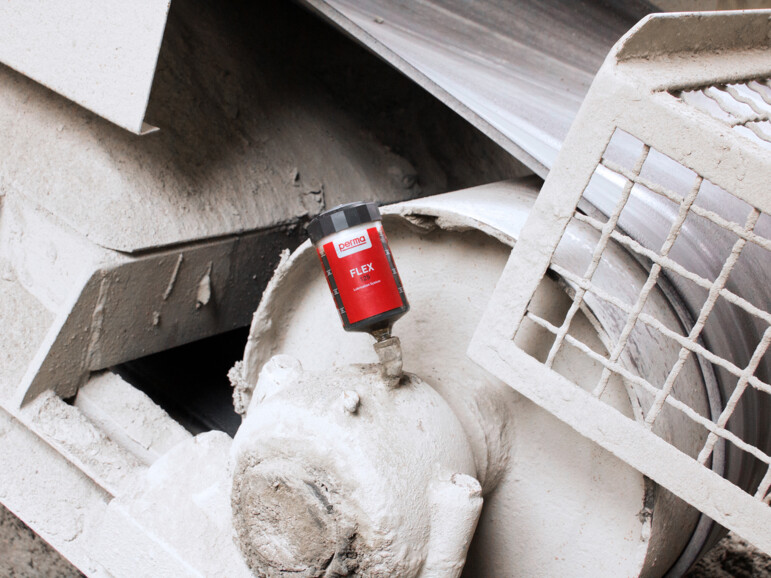
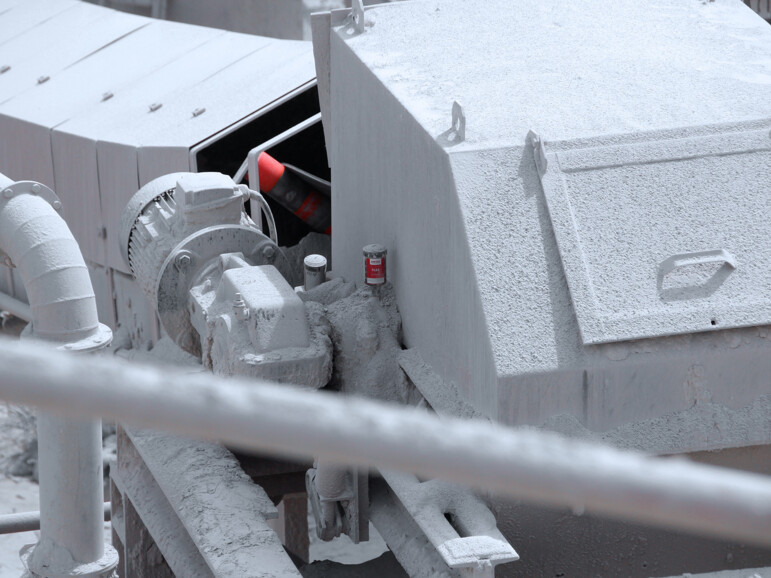